木製品を使ったノベルティをつくりたい
伝統の枡から、
枡を利用した
オリジナル商品まで、
幅広くご提案可能です
小ロット対応から
量産まで
お任せください!
このようなご相談に
お応えします
オリジナルの枡をつくりたい
SDGsや地産地消に配慮したノベルティをつくりたい
イベントのノベルティ用に量産できる業者を探している
小ロットから作ってほしい
大橋量器ができること
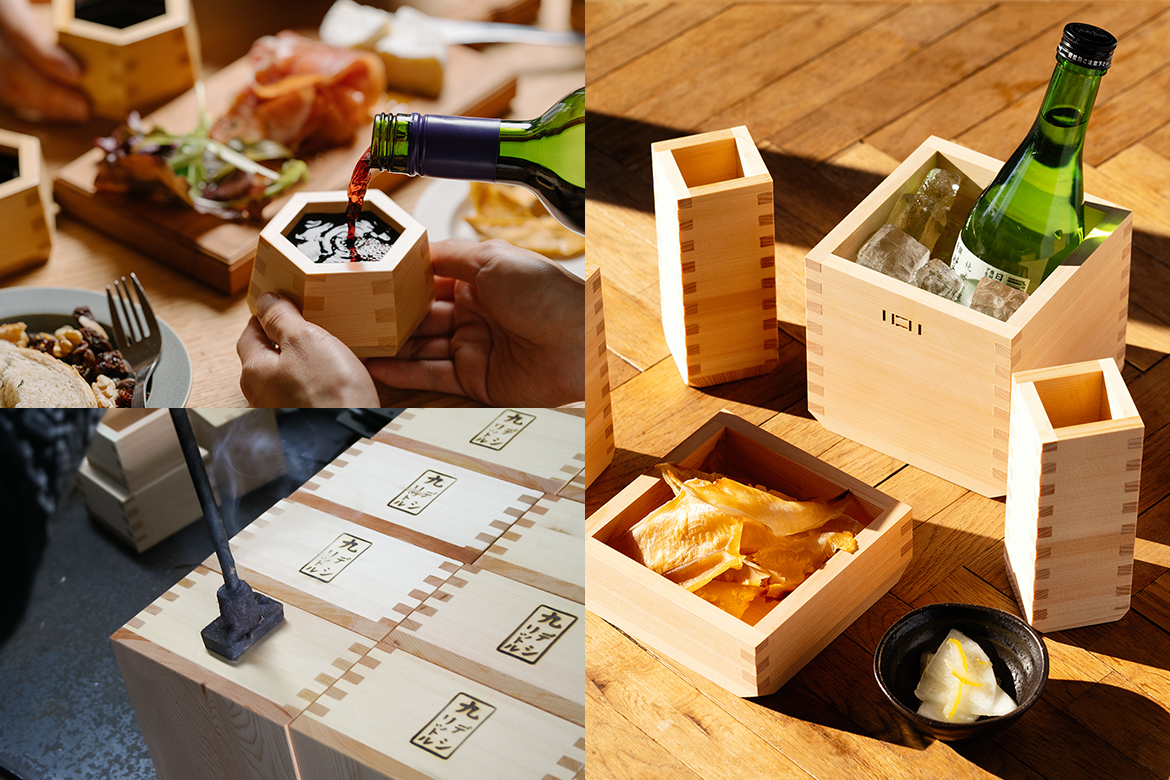
ご要望に合わせたご提案と
アイディアの実現
オリジナルデザインや名入れの方法は、「焼印・レーザー・シルクプリント」の3種類からお客様のご希望やご予算に合わせてご提案します。すべての名入れ工程を自社で行っているため、細かいご要望にもお応えできます。
焼印は写真製版できる腐食銅版を使用します。熱伝導に優れ、かつ高温に耐える銅版が、細かなデザインの表現力と低価格の両立を可能にしています。レーザー加工では、結婚式の席札として一人ひとりのお名前を印字したり、写真やグラデーションのあるデザインをそのまま表現したりできます。
「枡と枡を重ねてお重のようにしたい」「枡に蓋を付けたい」「八角形の枡がほしい」
こういった特注品へのご要望も対応しております。大橋量器は営業と職人の距離が近く、お客様のご要望に応じて職人と打ち合わせを行いながら、「お客様の希望を実現できる方法」をご提案できるように努めています。
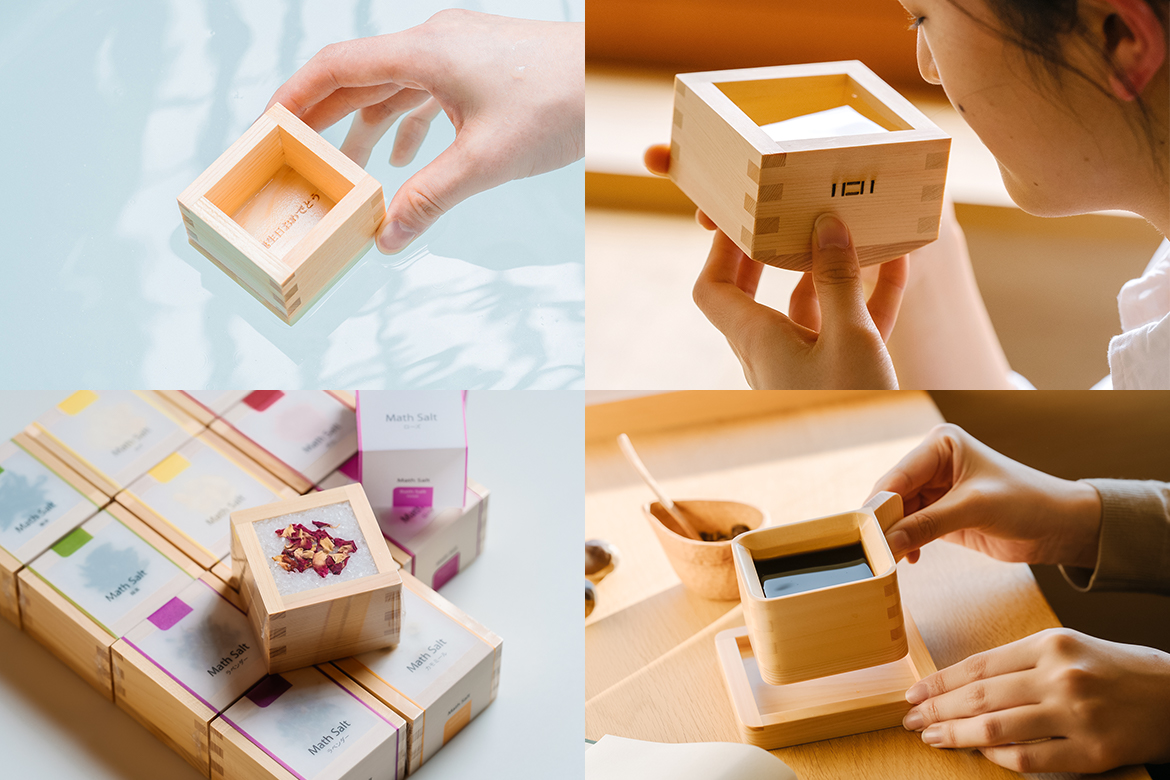
使用シーンを想像し、
人の声を取り入れる
商品開発
「使う人に幸せな時間を枡で味わってほしい。枡で幸せな空間を提供したい」
これが当社の目指す目的ですので、「使う人にとって幸せな時と場を創り出せる」と直感すればそれは当社の商品になり得ます。ヒノキのぬくもりや香りを伝えながら、暮らしの中で使いやすく心躍るような製品作りに努めています。
例えば「枡の入浴剤 Math Salt(マスソルト)」は、デザイナーの卵である美術学生と「枡でプチ感動を表現したい」という思いで開発しました。お風呂でホッとリラックスする時間にメッセージを受け取るプチ感動を味わえる商品として、年々人気が出てきています。枡と一緒に過ごす時間が尊いものだと確信しており、今も当社おすすめの自信作です。
人気のジョッキ枡やコーヒーカップは飲みやすいように口元を丸めたり、持ち手部分のサイズを調整したりと、お客さまの声を聞きながらアップデートを重ねています。2020年からは「アンバサダー制度」を導入し、商品開発の段階からユーザーの皆さまの意見を取り入れながら、より良い商品開発に取り組んでいます。
枡へのこだわり
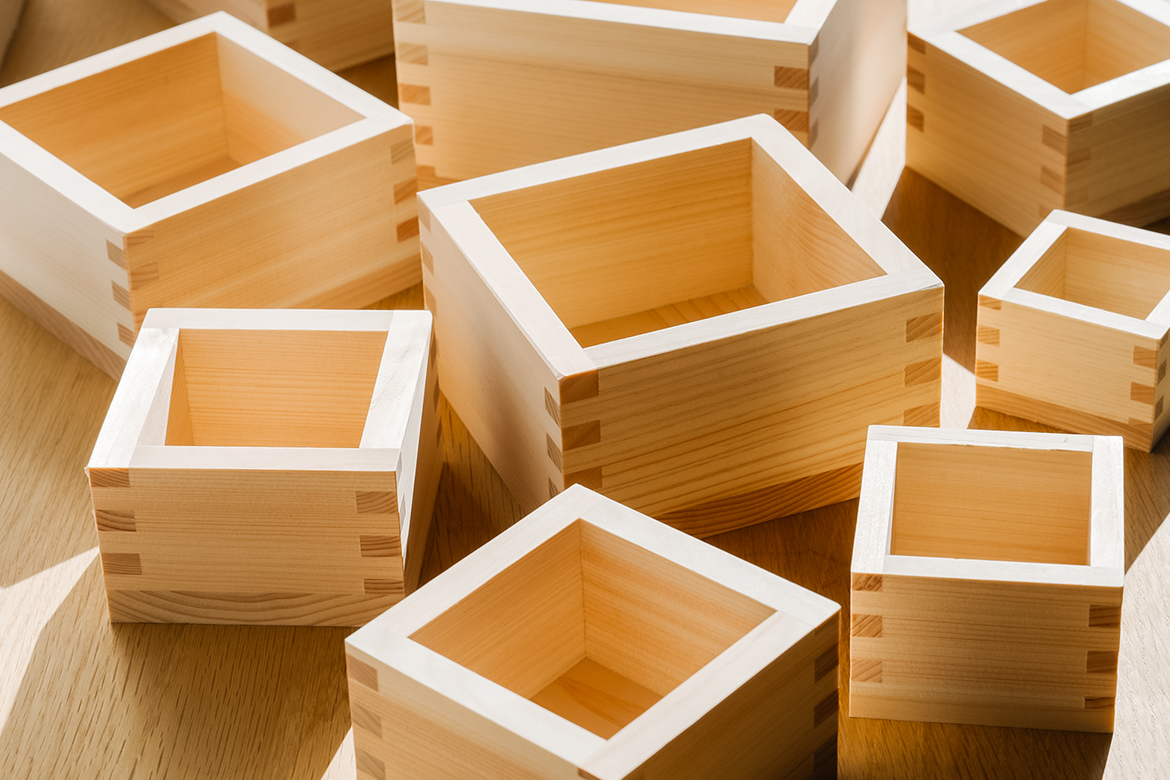
天然の国産檜を使用
わたしたちがつくる枡はすべて日本産。国内で採れた檜(ひのき)を使用しています。全体的に淡く、淡黄色に近い色合いは落ち着いた清潔感があります。天然素材だからこそ、一つ一つの木目も異なります。
- 木目:まったく同じの木目はひとつとしてありません。長年、森で育ってきた証です。
- 木色:丸太の内側「赤太(あかた)」と外側「白太(しらた)」違いで色が変わります。
- 木肌:高級木材であるヒノキは光沢があり、薄桃色・薄黄白色の白木です。やわらかでなめらかなその木肌は優しさとぬくもりを感じます。表面に汚れが付きにくく、まな板やカウンター等、食との相性も抜群です。
- 樹脂成分:桧の抗菌作用や、特有の芳香をもたらす成分が高温多湿時に表面化します。
- フシ:幹が太くなる過程の中で枝の元の部分が幹の中に包み込まれてできたものです。
- リラックス効果:檜は「香りを売る」と言われるほど特有の芳香があり、フィトンチッドという物質も含まれています。フィトンチッドには森林浴の時に感じる爽やかなリフレッシュ感、消臭防臭効果と抗菌・防虫効果、気分をリラックスさせてストレスを軽減させる効果があります。檜は私たちに癒しをもたらしてくれる木なのです。
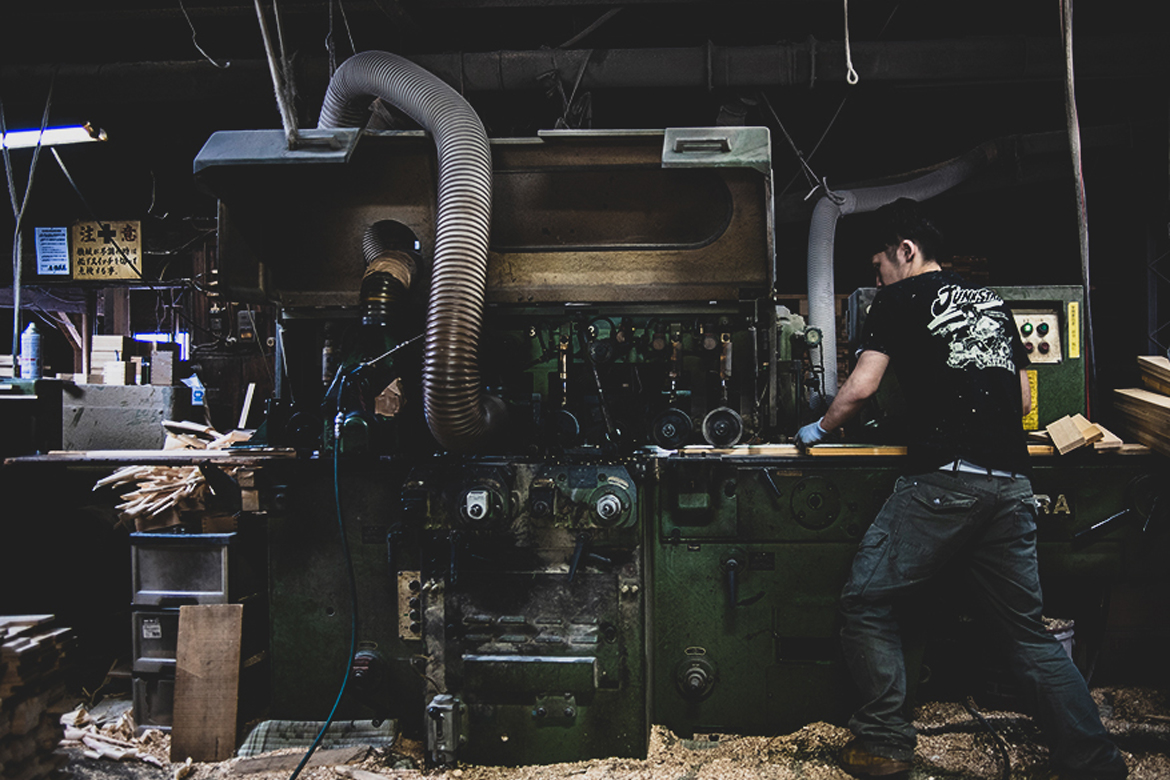
美しい仕上がり
伝統的な枡はシンプルな直方体ですが、その製作には緻密さが求められます。正確に切り出した4枚の側板を組み、底板を貼り、カンナをかけて仕上げる。機械を使いながらもさまざまな工程で繊細な手作業を欠かすことができない枡づくりは、枡職人の知恵と匠の技が生きています。
- 枡職人:枡をつくるための3要素は「檜」「道具と刃物」「職人」です。大橋量器の職人は伝統の規格枡を精度高く量産するのと同時に、新製品や特注の枡も、若い職人達のチームワークでつくり上げます。
- あられ組:枡の最重要ポイント。はかりとして活躍してきた枡にとって、形を強固に保つあられ組は大切な技術です。檜の特性を引き出し「木殺し」を施した組みは、液体まで保持できる性能と、枡の美しさを実現します。
- 円盤かんな:表面仕上げをすることで木肌の質感を際立てます。研ぎ澄まされた職人の手先の感覚と、円盤かんなの絶妙なハーモニーが、枡をつるっとしたなめらかな手触りに仕上げます。
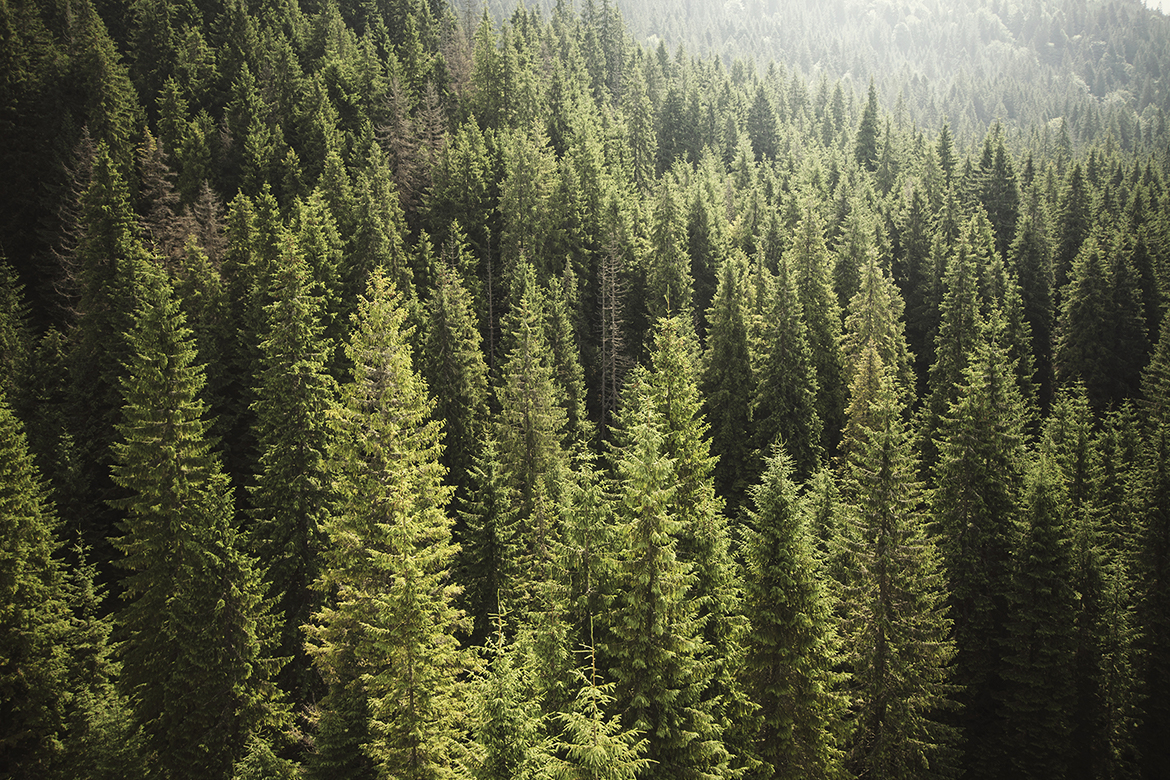
環境に優しく、
森の資源を活かす。
枡づくりに使用している木材は、住宅を建てるときに使用される建築材の端材を利用しています、枡を作るために伐採するのではなく、使い道の限られた木材を使用することで、森づくりの一端を担っています。
- 端材活用:端材とは切り落とされた「端っこの材料」のこと。サイズが豊富な枡づくりに生かします。
- 使い切る:枡をつくる工程で出る木の削り節を商品を届けるときの緩衝材に使用しています。
- SDGs:環境保全に類するエコな製品づくりに専念しており、環境に負担をかけない脱プラスチックに取り組んでいます。森林育成に貢献することで山から川へ栄養が行き渡り、海の環境保全につながります。
SDGsとは「持続可能な開発のための2030 アジェンダ」にて記載された、2030年までの国際目標のことを指します。
受賞歴
枡ができるまで
木材の仕入れ
大垣市は、木曽や東濃など日本有数のヒノキの産地に近く、良質の天然桧を入手するには恵まれた土地です。
ただ枡をつくるために木を切るのではなく、家を建てる際の柱やかもい、なげし等を作る際に出る切り落とし部分(端材)を材料として仕入れています。枡は林業のサイクルに根差した、環境にやさしいエコな道具なのです。
乾燥
乾燥させて木の水分や油分を散らします。 木の収縮を少なくするため、ヤニを出にくくするためにとても重要な工程です。一升枡のような面の広い材料ほど木の反りや変形が出やすいため、乾燥させる際も気を配ります。
天日干しや乾燥場の燻し、電気ヒーターなどを使い分けており、天日干しの場合は冬に仕入れた材料も夏まで待って、ひと夏干します。
モルダー
4軸モルダーで桧の板材の下面・右面・左面・上面を同時に削り、4面の表面を加工するためのサイズに整えます。一合枡だけでも、一日におよそ1600枚の側板用の板材と、400枚の底板用の板材をモルダーに通しますので、一日あたり、約2000枚の桧の板材を掛けることになります。
モルダーの出口には「超仕上げ」と呼ばれるかんな掛けをする大きな機械があり、枡の側板の場合は内側になる面をツルツルにかんな掛けします。
駒切り
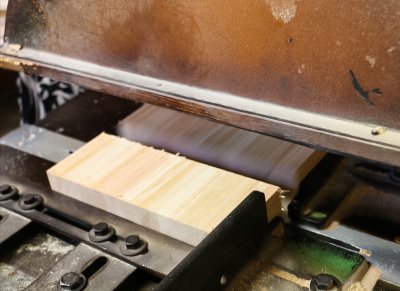
カッター
ロッキングカッターで枡の組目となる溝(ほぞ)を掘る工程です。
回転する複数枚のカッター(丸鋸チップソーの幅の広いモノ)が等間隔に並んでいるところに、ロックされた駒が上下動させます。一度の上下動で左右対称となる20枚の溝が掘られた駒ができます。
のり付け
溝(ほぞ)ができた駒の溝の間に、ブラシで糊を塗ります。多すぎず少なすぎず均一な量になるよう気をつけながら、20枚をまとめて塗っていく様はまさに職人技。大橋量器では、食品安全衛生上問題のない木工用ボンドを使用しております。
組み(仮組・本締)
糊付けされた状態の駒4枚一組で四角に組み、軽い圧を掛けて仮組します。 一合枡の場合は機械で、一合枡・八勺枡より大きいものや小さいものは手組みで行い、その後に本締めをします。
エアーの圧力を利用した締め機で締め上げながら、締まっているかどうかは目視でチェックをしていきます。組む速さや締める感覚は、熟練した技術が必要な工程です。
底付け(手締め・底付け機)
完成した木枠に底板を貼り付ける工程です。組みで使用するものと同じ糊を木枠に付けて底板を貼り付け乾燥させます。手作業で締めて一晩乾燥させる方法と、底付け機の熱で乾燥させる方法があります。
ここで初めて枡の原形が完成し、この状態で保管します。
仕上げ削り
円盤カンナと呼ばれる機械で側面の4面を一気に削ります。ぐるぐる回るかんな削りの機械にはカンナ刃が3枚ついており、作業台面と回転している円盤面が垂直になるよう当てて削ります。熟練した職人が均一・ピカピカに仕上げる枡づくりに特化した独自の工程です。
面取り
製品の角を丸め、それを扱う人にとってやさしい手触りや口当たりにする作業です。円盤カンナで仕上がった枡の角部分を手がんなや面取り機で取ります。一つ一つ枡の全12辺の面を取り、枡が完成します。手がんなで面取りする技は枡職人の腕の見せ所です。
焼印・レーザー・印刷
枡にはオリジナルデザインや名入れを施すことができます。焼印・レーザー・プリント(シルク印刷)の3種類があり、それぞれ特徴が異なりますのでお客様のご要望に応じて決定します。
焼印は専用の焼印機にデザインされた銅版を設置し、高温で圧を掛けて枡に焼き付けます。レーザー加工に比べて、焦げ色が濃くはっきりと押印されるデザインが特徴です。
梱包・出荷
完成した枡を一つ一つチェックしながら大切にクラフト紙で包装し、箱詰めして出荷します。
檜の香りと共に、皆様にお届けいたします。